- Sealing materials
- Coating materials
- Conductive pastes
- Insulating pastes
- Solders
- Adhesives
- Printed circuit boards
- Circuit substrates
About “Kakuhunter“
It is a planetary centrifugal mixer that can solve your problems and meets your needs for any industry, for any material, and for any application.
“First, what is a mixer?”
- Simultaneous mixing and defoaming!
- For diverse range of materials!
- For high-precision mixing!
Development History
In the 1990s, with the miniaturization of electronic components, there was a demand for precise mixing of electronic materials and high-precision defoaming of bubbles mixed in during mixing.
In order to meet the needs, we began developing an industrial planetary centrifugal mixer with excellent versatility and durability that enables precise simultaneous mixing and defoaming. In 1992, we launched “the SNB Series (now known as Kakuhunter),” a high-spec planetary centrifugal mixer equipped featuring the first Individual Revolution and Rotation Speed Control system.
The most significant challenge during development was “what the ratio of revolution to rotation should be.” Initially, we started development with two motors, but then we moved on to developing a variable ratio function with one motor to create a machine with a wide range of revolution and
rotation speed settings. Since then, we have developed a large-sized machine with improved throughput, a vacuum unit type with an improved defoaming effect, and a compact entry model to meet market needs.
Through research and development each and every day, Kakuhunter continues to pursue new value.
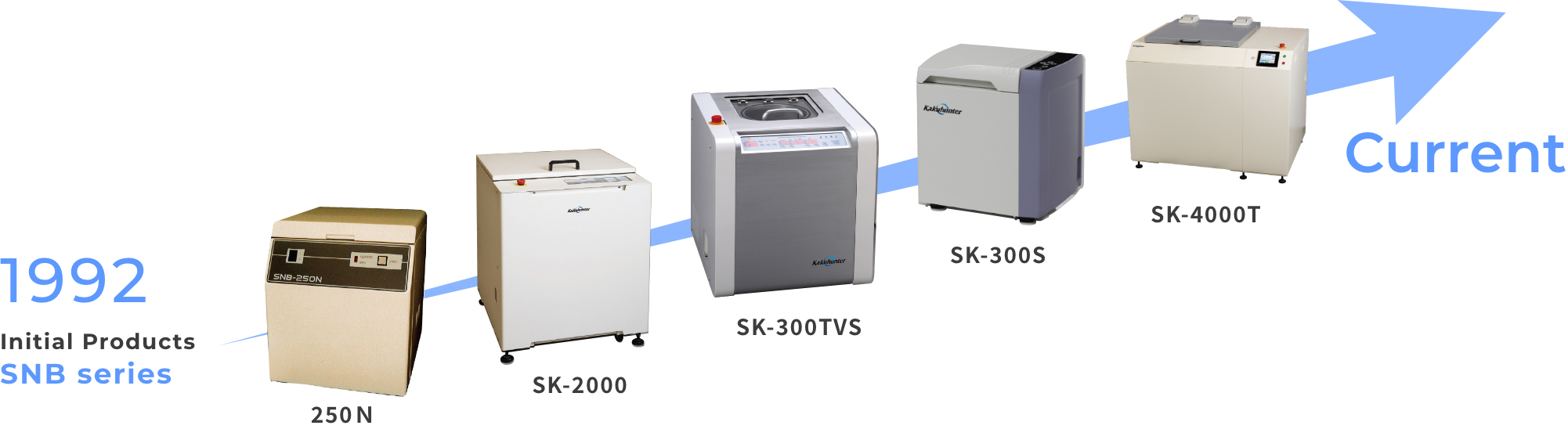
01Features
Kakuhunter’s Mixing Mechanism
Kakuhunter is capable of uniform mixing and fine defoaming for a diverse range of materials from low viscosity to high viscosity.
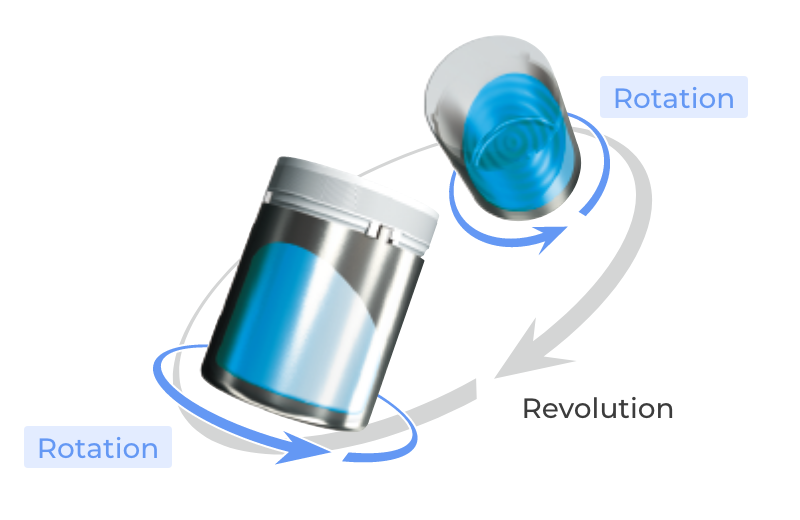
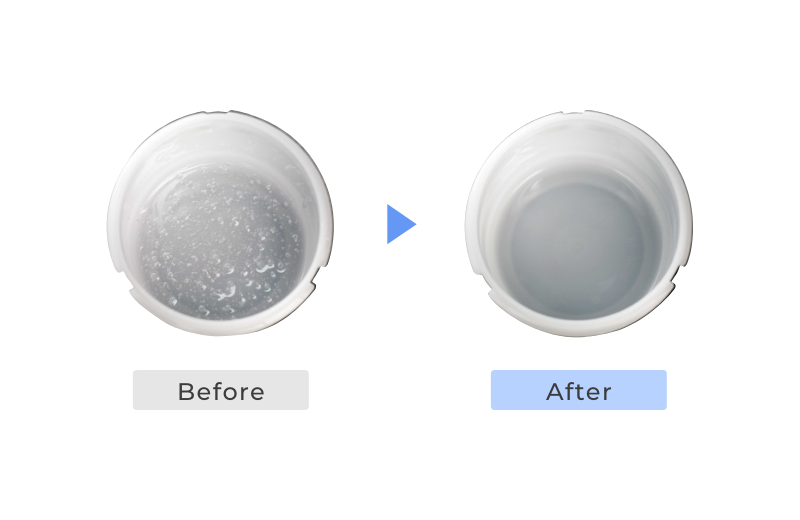
Differences from Other Methods than Revolution-rotation Type
Other major mixing methods include “propeller type,” “roll type,” and “roller type,” but they have various problems such that: “mixing requires a lot of time;” “materials are damaged;” “precision mixing cannot be performed;” “there is a need for cleaning;” and “defoaming cannot be performed.” On the other hand, the revolution-rotation type can uniformly mix and completely defoam a diverse range of materials whatever their viscosity as both the container and the machine are sealed, causing no foreign matter to be mixed in, with no damage to materials, where continuous work accompanied by material changes can also be performed smoothly.
Six Major Features of the Revolution-Rotation Type “Kakuhunter”
-
Feature01
Short-time Mixing Capability
All sorts of materials from low viscosity to high viscosity can be mixed and defoamed in just a few tens of seconds to a few minutes
-
Feature02
Simultaneous Processing of Defoaming
Defoaming is performed by the centrifugal force of revolution and with the bubble breaking effect by film formation between container sidewalls and materials
-
Feature03
No Damage Caused to Materials
The planetary centrifugal mixer does not cause damage to materials since there is no contact between the machine and materials.
-
Feature04
Suppression of Temperature Rises
Temperature rises by mixing can be suppressed by optimizing the operation pattern.
-
Feature05
Easy Cleaning of the Machine
Since there is no propeller, there is no need for cleaning of the machine body and no loss of materials.
-
Feature06
User-friendly Operation Screen
Operation settings can be easily made by using the up/down and right/left keys on the control panel only.
02Applications / Capabilities
Can be used across a wide range of fields, for wide-ranging applications, and a diverse range of materials
Kakuhunter has been dramatically improved in the precision of mixing, dispersing, and defoaming in step with technological advances in the market. Therefore, it can be used for mixing and defoaming a wide range of materials in various industrial fields whatever their applications may be.
Field Examples
-
Electronic Materials
-
Chemical Materials
- Carbon nanotubes
- Carbon fibers
- Carbon blacks
- Ceramics
- Urethane resins
- Silicone resins
- Acrylic resins
-
Energy Materials
- Fuel batteries
- Electrode materials
- All-solid-state batteries
- Secondary batteries
- Solar panels
-
Automobile-related Materials
- EVs
- Batteries
- Fuel batteries
- Tires
- Greases
- Adhesives
- Heat radiating materials
- Paints
-
Medical Materials
- 3D shaping
- Dental materials
- Endoscopes
-
Semiconductor-related Materials
- Ceramic members
- Adhesives
- Machine parts
- Transfer machine parts
-
Imaging-related Materials
- Organic EL displays
- Liquid crystal displays
- LED displays
-
Cosmetic Materials
- Foundations
- Lipsticks
- Nail polishes
- Eyeshadows
- Hair colorings
Application Examples
-
Mixing
Material: Printing ink
-
Defoaming
Material: High-viscosity adhesive
-
Dispersing
Material: Fluorescent powder + Resin
-
Crushing
Material: Colored stone
(Zirconia balls used) -
Kneading
Material: Clay
-
Separating
Material: Adhesive + Colored stone
-
Emulsifying
Material: Egg + Oil + Vinegar
Compatible with various cases
03Unique Functions / Operation Settings
Individual Revolution and Rotation Speed Control System
The performance results of mixing and defoaming vary greatly depending on the ratio of revolution to rotation, respective speeds, and combination of step operations, etc. Kakuhunter can change the ratio of revolution to rotation and set up to 90 rotational patterns. In conventional models, the ratio of rotation is fixed, and even if the speed of revolution is adjusted, there are issues such as a failure in mixing and formation of lumps. On the other hand, Kakuhunter can be set to 9 revolution steps and 10 rotation steps, making it possible to solve issues with fixed rotation ratio types.
Examples of Other Unique Functions and Operation Settings
-
- Step Operation
-
Step operation enables continuous running of multiple different operation patterns.
Step operation can be set for each model to meet various mixing and defoaming needs.
-
- Special Mode
-
Depending on the machine, special modes compatible with materials can be selected.
-
- Liquids and powders are blended together, then suppress the formation of lumps.
-
- Aggregation and separation are suppressed to accelerate dispersion.
-
- The rotation speed is increased and decreased to accelerate mixing.
-
- The rotation speed is decreased to the minimum to remove fine bubbles.
-
- The separation of materials with specific gravity differences is suppressed.
-
- Gives priority to defoaming at high speed.
-
-
- User-Friendly Control Panel
-
With its innovative design and user-friendly control panel, it contributes to efficient mixing and defoaming across a wide range of situations, from research and development to mass production.
- Vacuum Level Display Section
- Vacuum Manual Switch
- Vacuum Breaking Valve Switch
- Vacuum Control Valve Switch
- Progress Bar
- Channel / Step / Revolution
Display of data such as rotation time error - Data Setting Switch
- Precaution (icon) Lamp
· Mishandling Prevention Key Lock
· Cover Open
· Vibration
· Maintenance - Data Determination / Error Reset Switch
- Start / Stop Switch
-
- Vacuum Reduced Pressure Function
-
The vacuum reduced pressure function makes it possible to eliminate even ultrafine air bubbles from the materials; therefore, this function can improve the conductivity and insulation properties required for electronic materials, improve the yield rate by removing bubbles in optical materials, and prevent the injection of air owing to air bubbles in syringes.
In addition, by placing a vacuum pump separately, we offer multiple options and improved maintenance efficiency.Only during vacuum pressure reduction operation is the vacuum chamber shut off, and only the rotor part is depressurized. The vacuum can be set arbitrarily (up to 1.3 kPa) while the vacuum pressure reduction is monitored. * This machine can also be used as a vacuum desiccator without rotating.
-
- Vacuum Control System
-
On Delay
- By delaying the timing to draw a vacuum, temperature increases and changes in material composition can be suppressed.
- Scattering of fine powders when mixing fine powder and liquid is suppressed to prevent powder adhesion to the container lid, insufficient mixing, and insufficient dispersion.
Off Delay
- By delaying the timing at which vacuum operation is terminated, bubble entrainment until rotation stops can be eliminated and defoaming precision can be improved.
-
- Shifted Cup Tray
-
Mixing Ability Improved with the Adoption of Shifted Cup Trays on the Rotation Axis!
Since cup trays on the rotational axis are shifted to increase the contact surfaces between containers and materials, compared with conventional machines (cup tray facing), mixing performance is improved.
Furthermore, effective mixing can be performed since long containers can also be set, maintaining a distance from the revolution axis to apply centrifugal forces to the whole.Comparison of mixing time (straight rotor vs shifted rotor)
-
- Communication Function
-
Operation data such as operating time, mixing conditions, and temperatures can be saved and used for traceability.
-
- Optimum Settings
-
The rotational speed can be set to 9 steps for revolution and 10 steps for rotation, and 90 patterns can be made by combining both.
As a memory channel (conditions setting memory), it is possible to set 90 user-settable channels and 10 fixed data channels, which contributes to efficient mixing and defoaming across a wide range of situations, from research and development to mass production.
Inquiry / Brochure Request
For inquiries about our service and products, contact us from the link by clicking on the button below.
* You will be redirected to a page on another domain managed by us.
We have made available a brochure with detailed information about Kakuhunter and catalogs for each product model.
* You will be redirected to a page on another domain managed by us.
Developed and distributed by:
SHASHIN KAGAKU CO., LTD. Product Company
Weekdays 9:00 a.m. ~ 5:00 p.m. (closed on Saturdays, Sundays, and holidays)